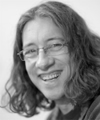
Not much can go wrong with a KNX installation, but if an electrical fault does develop, Simon Buddle explains why it makes sense to have the right diagnostic tools in order to save time and money.
During the summer of 1987 I purchased, what turned out to be, the one and only car I would ever own in my life, so far. A cherry-red Datsun Sunny. I drove the car until it would drive no more. I polished it, changed the oil, repaired the heater, and changed the alternator, spark plugs and clutch cables. By the time it finally met its rusty demise I knew every inch of it and could fix anything on it. A Haynes manual and a tool bag were all you needed.
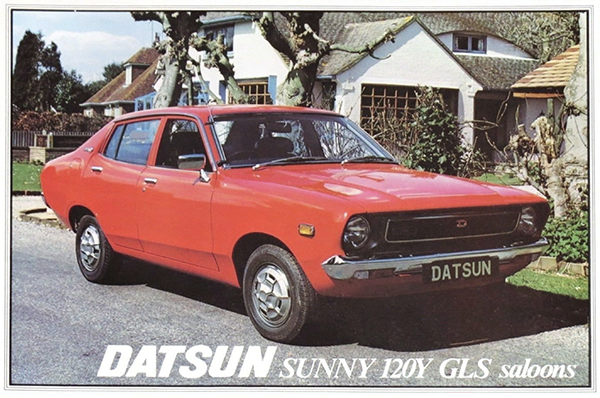
Lift the bonnet of a modern car and the story is completely different. Unless you have the relevant diagnostics software and a USB lead there is no chance that you will be able to find the problem, let alone fix it.
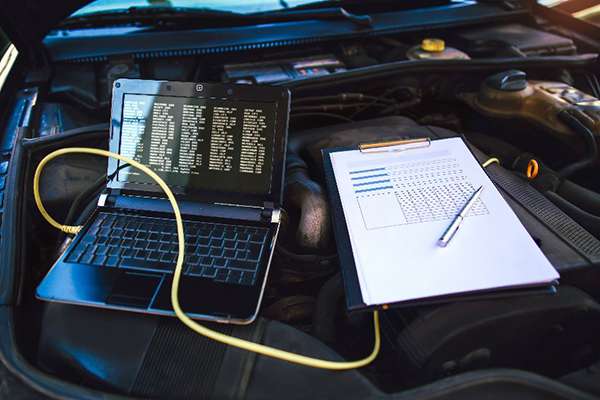
KNX is robust
One of many reasons that I love KNX is the robust nature of the KNX bus. You can wire it in almost any configuration. If needs, be you can grab a data or security cable to extend the bus to a location that does not have a KNX bus cable. It runs over IP, RF or Powerline. It is amazing. The distributed intelligence means that even if one device fails, the rest of the system keeps running as normal.
Sufficient power
Power calculations should be part and parcel of KNX system design; how many devices and what the bus current draw is per device. If I have forty Jung Room Controllers in my project at 20mA each, I have a projected load of 800mA. That is before we start to look at the actuators and other devices on the bus. So, we need to size my power supply accordingly and look to break the installation down into a couple of lines, adding one or maybe two additional power supplies.
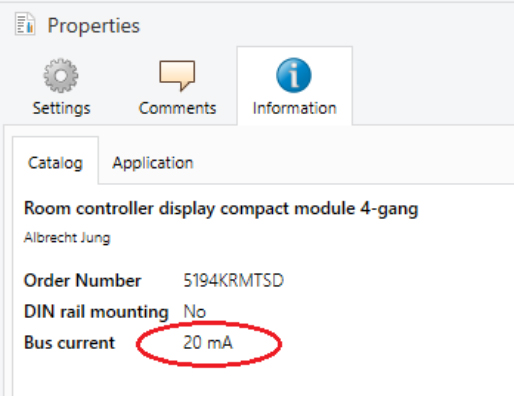
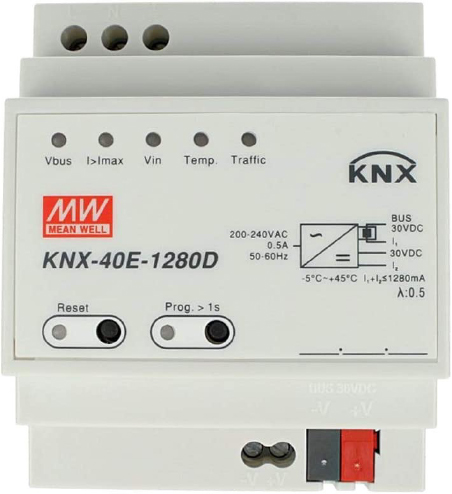
What’s under the hood?
Like modern-day cars, it can be a challenge to understand what is happening on the KNX bus. Due to the robust nature of the bus, it is true to say that we rarely have problems with data transmission being corrupted. We can see the data through ETS Group Monitoring. On the rare occasion that data is corrupted, we might use an oscilloscope attached to the bus. This can read the digital waveform being transmitted and hopefully enable us to find corrupt data. So rare are these occurrences that it makes the scope feel like an expensive purchase. However, it is more common to see power related issues. Voltage drop is easy to measure but bus current draw can be trickier.
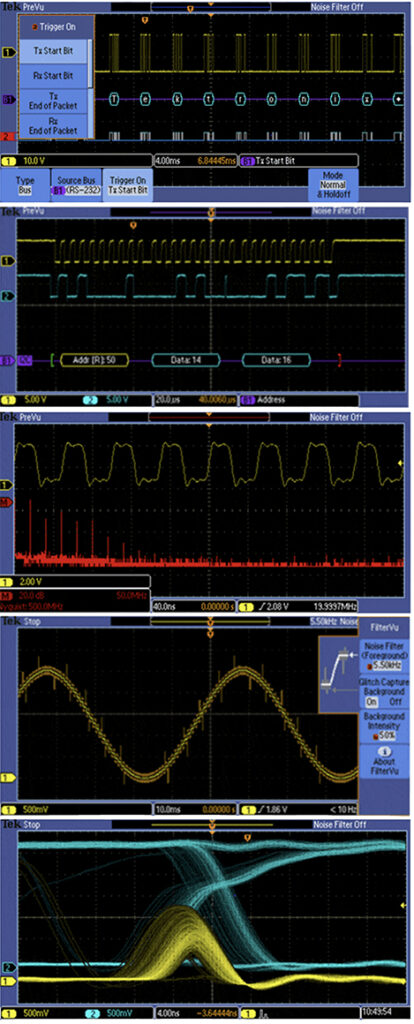
Power supply diagnostics
There is value in using a power supply that includes diagnostic capabilities. That will show you if you have problems on the bus. The three most obvious and useful items that you can monitor are bus voltage, bus current and bus load. But two other important pieces of information come in the form of overloads and short circuits. If the bus has a permanent overload or short circuit, that will get addressed during installation. But there are those times when the system seems fine but just occasionally performs erratically, possibly a cable end has not been made safe, leading to occasional short circuits on the bus. If you have visibility of the problem, you have a route to resolving it.
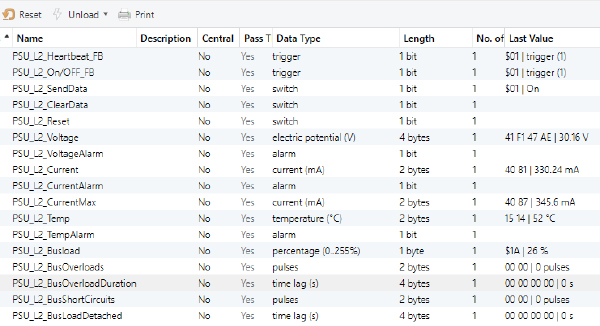
We should always ensure that our power supplies are working at no more than 80% capacity. The value of the power supply diagnostics cannot be overstated. Even if you keep it on the shelf as a service tool to help identify issues, it will save you time and money. If you do permanently install the diagnostics PSU, you can of course setup email alerts for any of the parameters that will increase the speed with which you can identify and resolve the problem.
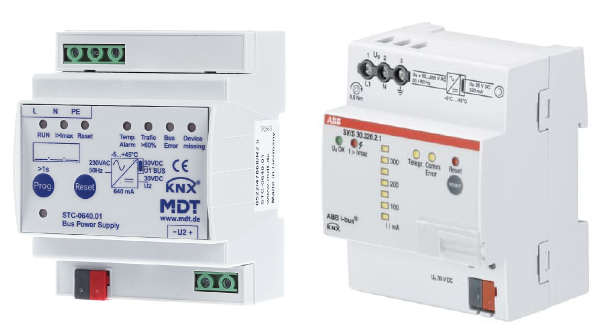
Conclusion
Service calls are expensive, and service calls to intermittent problems are hugely expensive. For the customer, it represents a system that does not work and a dealer who cannot identify or fix it. The sooner we solve the problem the better for all concerned. Like all faults or problems, the more data we have, the easier it will be to solve.
Empirical data from bus diagnostics provides the visible evidence to electrical issues that may be causing faults. The best that can happen with this data is that we do not need it, but without it, we are simply guessing. The price of a diagnostics power supply is less than the cost of a call-out. For me, that is a simple equation. It also makes us more professional at fault finding as well as informing our choices next time round during the design process.
Simon Buddle CEng MIET, is a consultant for Future Ready Homes, a specialist in BMS and ELV services system design.