By Mark Warburton, Ivory Egg.
The KNX stand at the ISE show last week was constantly busy with integrators from around the world wanting to find out more about KNX and the products from manufacturers. It’s always great to support both new and existing integrators as they deliver KNX projects, and during the show, I had the pleasure of presenting a talk on some of the common mistakes made on KNX projects and how to solve them. However, as not everyone had the luxury of attending the show, here are some of the key issues we see on KNX projects.
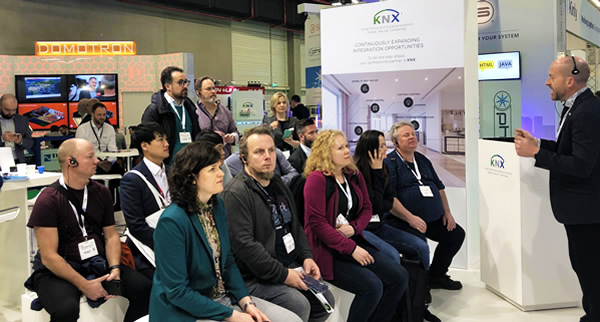
Using lots of manufacturers
This may seem counterintuitive, given one of the key benefits of KNX is the wide range of manufacturers to choose from. Even within a single manufacturer, there can be countless products that all do a similar job. And whilst the KNX standard does ensure all products work together, manufacturers are free to define how products work, as well as the labelling of objects and parameters, which can be confusing. So, by keeping the bulk of a project to one manufacturer, you can ensure the project is quick and easier to deliver, program and support, as all parameters, labelling and functions will be consistent.
And if you can stick to this from project to project you will save even more time, making the project more profitable. We usually see about 90% of a project delivered using products from one or two manufacturers, with the last 10% made up of a mixture of manufacturers where a specific solution is needed, such as interfacing to the AC units or plant room.
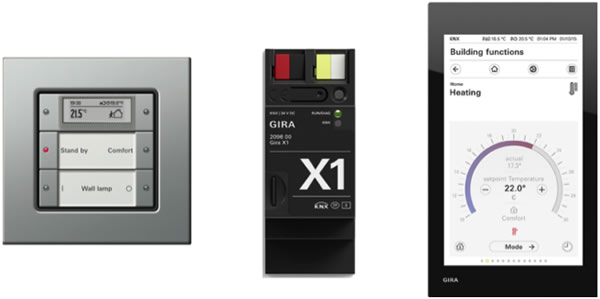
Group Address naming
There are two common approaches to Group Address naming; namely room-based and function-based. More information on this can be found in this guide
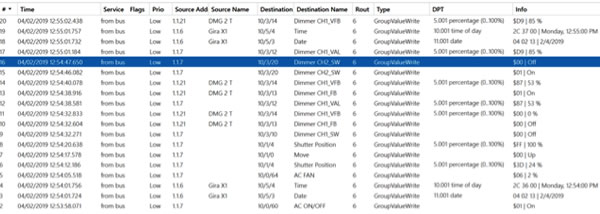
Lack of a clear functional specification
KNX is one of the most functional systems in the world, which isn’t surprising given the number of products and applications for which it can be used. Even something as simple as a keypad can be configured in countless ways, so it is crucial that the way the system is going to work is clearly planned and documented. This is, however, often overlooked and the system just programmed ad hoc. Even when it is planned, it’s common for the homeowner to start requesting changes before the system is even completed. All of this can lead to a system that is never really finished, because there isn’t a clear finishing line.
Whilst giving the customer a chance to customise the system is key, a better approach is to define a clear base functionality in the system and then make changes once the system is complete and the project officially finished. This gives the customer a chance to live with the system, and provides a point to return to if there are any problems.
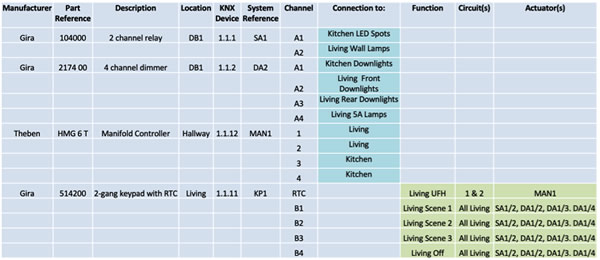
Power consumption
It seems fairly obvious that working out the power requirements of the KNX devices in a system would be a key step in the design of a projects, but it is surprising how often this is overlooked. As there is a maximum of 64 devices in a segment, and most power supplies are 640mA, device power consumption is often estimated at 10mA. However, there are many devices on the market that consume much more than 10mA, so it is essential to check the loadings and either reduce the number of devices in the segment, or use one of the larger power supplies on the market. It’s important to remember that the 64 device limit exists regardless of the size of the power supply, as it is based on maintaining the integrity of the telegrams in order to ensure that the system is reliable and robust.
Conclusion
The above is a starting point to making sure that your projects are delivered effectively and profitably, but there is always lots to learn. The KNX Association has some great guides on its website around project delivery and there are other resources, such as the Ivory Egg knowledge base
Mark Warburton is the Technical Director of Ivory Egg (UK) Ltd, a supplier of leading KNX products and provider of KNX training courses.