By Mark Warburton, Ivory Egg.
It’s getting cold out, well in the Northern Hemisphere anyway, so it must be time for an article about heating control. The decentralised nature of KNX makes it ideal for heating control, particularly in systems with many zones and device types. Integrating UFH with radiators for boost, along with air-conditioning with window contacts to disable, sounds complicated, but is actually fairly straightforward thanks to the intelligence found in most KNX thermostats. However, although KNX is standardised, room temperature control is one of the areas where there are some large gaps between manufacturers in terms of functionality and user control. Nonetheless, there are some common threads across all manufacturers, so let’s have a look at those aspects first.
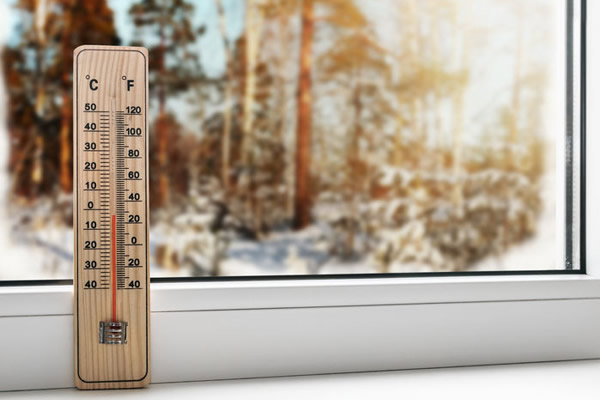
Temperature Sensing
There are two main options when considering KNX thermostats:
• Keypad with integrated temperature sensor and regulation. This will output a demand signal based on the defined set point and temperature. The keypad may have a display to change the set point, or alternatively, this will have to be set from a separate user interface.
• Keypad with integrated temperature sensor only. This will have to be sent to a separate regulator, often found in a manifold controller, which will then output the demand signals or use them internally. With no display, a user interface will have to be provided elsewhere on the system in order to change the setpoint and for feedback.
Although the thermostat is generally fixed beside the door, which isn’t ideal given the airflow, there are a few ways to compensate for this:
• Calibration – all KNX temperature sensors have the ability to offset the temperature. Once an accurate temperature from the room is obtained, the sensor value can be calibrated in the device parameters.
• External temperature sensor – this allows a temperature from elsewhere in the room to be combined with the thermostat or even to replace it. As most KNX switches now have a built-in temperature sensor, you can read the temperature at each end of the room creating a more representative reading.
Multiple Stages
The majority of KNX heating regulators support 4 stages of heating and cooling:
– Heating Basic
– Heating Additional
– Cooling Basic
– Cooling Additional
Each stage has a separate output and defined thresholds for use. For example, a 2-stage heating situation might be defined as follows:
– Set point = 20º
– Additional Band = 2º
– Primary Source = UFH
– Secondary = Radiators
If the temperature falls below the set point less the additional band (20-2=18), then the radiators will be used until the temperature rises. In this way the room temperature will be constantly maintained in the most comfortable way possible.
There will also be a dead band between heating and cooling to prevent the two systems competing with each other. The system can either be set to automatically switch between heating and cooling or require manual change over.
Relative Mode Changes
The concepts of using modes to adjust the setpoint instead of changing the setpoint directly has long been a feature of KNX thermostats. It provides a simple way to decrease the setpoint across the whole building without defining specific setpoints in each room or zone.
The standard format uses an offset from a base setpoint.
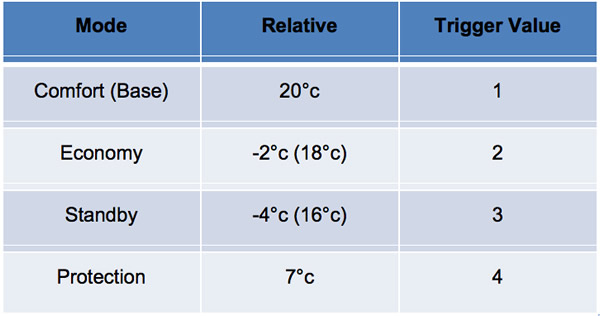
This concept works really well when the user is aware that the system should be changed to Comfort mode before changing the setpoint. However, a lot of customer struggle to understand the concept particularly in countries where changing the setpoint is the usual method. This leads integrators to offer both the mode change function and the ability to adjust the setpoint. For this to work correctly the thermostat has to be changed to Comfort mode before the setpoint is adjusted, otherwise the setpoint will get out of sync. This is usually left for the customer to understand, which, needless to say, can have mixed results.
There are a couple of solutions to this, but it is at this point that manufacturers’ opinions on the best solution can differ. In fact, it is a stark reminder of some of the problems found in systems that don’t have such strict standardisation as KNX!
Setpoint Shift
This method uses an increment/decrement value to shift the setpoint up or down without actually defining the value. This works really well and is by far the simplest solution, however, manufacturers can implement this differently, such as using a 1-bit object with 0 to decrease and 1 to increase, a 1-byte value in a similar way, or a 1-byte value used as an addend or subtrahend. It would be a great step forward if this became a standardised DPT (DataPoint Type), so here’s hoping someone from the KNX Association is reading.
Absolute Modes
Another approach is to use fixed values for each mode instead of the setpoint being referenced back to the base, comfort setpoint. This goes some way to simplifying matters for the customer as the can change the setpoint at will but it is difficult to manage the dead band when using Auto changeover between heating and cooling so its application can be limited. It is also only support by a few manufacturers so can present problems if you are looking to use visualisation to control setpoints.
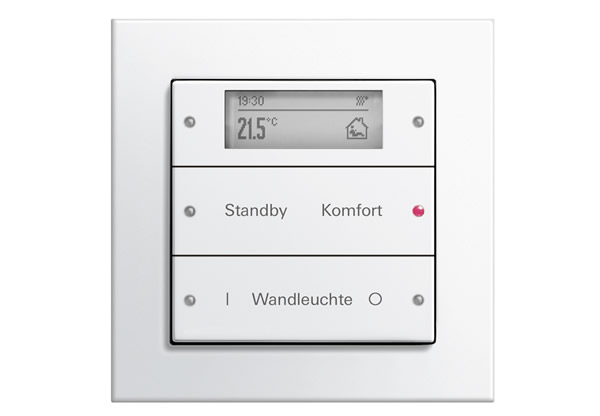
Simplified control
Some manufacturers are introducing simplified mode changes which allow you to reduce the number of modes presented to the customer, or just allow the setpoint to be changed. In fact, this is the solution often offered by integrators, particularly in modern, well-insulated buildings with large amounts of thermal mass. As it takes so long for heat to be lost, or to warm the fabric of the building, it is often more efficient to maintain a fixed setpoint for 24 hours instead of decreasing the setpoint overnight. The system can then be switched from the maintained temperature to a protection temperature when the building is vacant for longer periods, so only two modes are required.
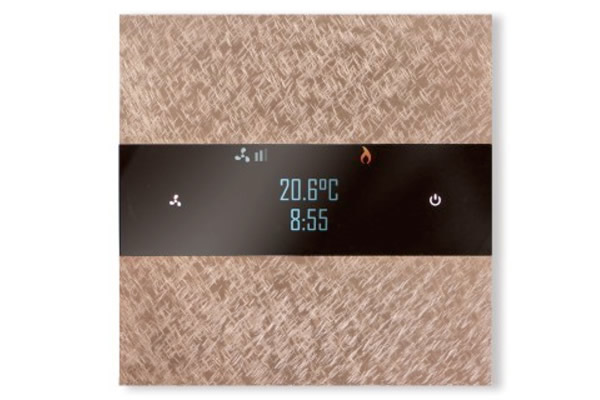
Additional Logic
Most of the issues with the above are caused when linking to visualisation or third-party AV systems. Some systems go further than others and have different profiles based on the thermostats used in the system, but either way. as long as you have a logic controller in the system, you will have the flexibility to integrate different mode types or convert values from one type to another.
Conclusion
Although this aspect of temperature control with KNX can be complicated, it shouldn’t detract from the fact KNX still offers one of the most flexible solutions for HVAC control. With native integration of so many device types, including UFH, radiators, fan coils, air-conditioning, chilled ceiling, electric heating to name just the obvious ones, and by the far the most extensive range of user interfaces in an endless array of design options, it remains the best option for the majority of installations.
Mark Warburton is the Technical Director of Ivory Egg (UK) Ltd, a supplier of leading KNX products and provider of KNX training courses.