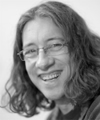
Simon Buddle explains how using the correct labelling helps to make KNX panels safe for everyone to use.
It’s difficult to comprehend our world if you are looking in from the outside. We have at our fingertips one of the great control systems of our time. The possibilities with KNX are nearly endless, and I won’t bore you by listing them. Even the most basic system can perplex a non-technical person. Show them a KNX control panel, and watch the look of confusion descend over their face. ‘But what is it and what does it do?’ may well be muttered. And, of course, the reply, ‘It controls the whole house’ doesn’t go any way towards answering the question; if anything it only serves to compound the confusion.
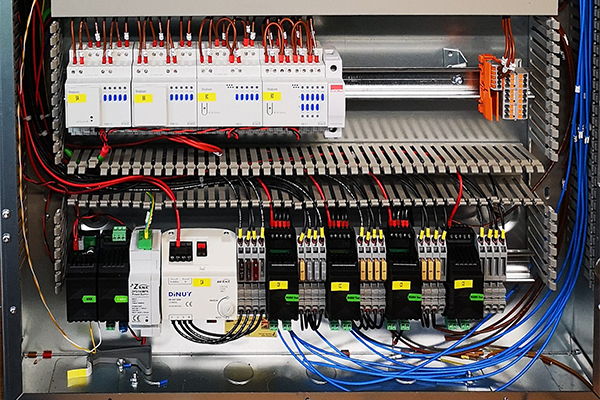
We tend to do an excellent job of technical design documentation, and this feeds through to labelling cables in the field. That in turn informs panel build requirements, and even in the panel, we can see markers used to identify the internal panel cabling. But how much information is too much? For me, there is never too much information. Each panel should have, as a minimum, a label for every channel as well as a laminated document detailing, by electrical breaker, which modules and channels are controlled.
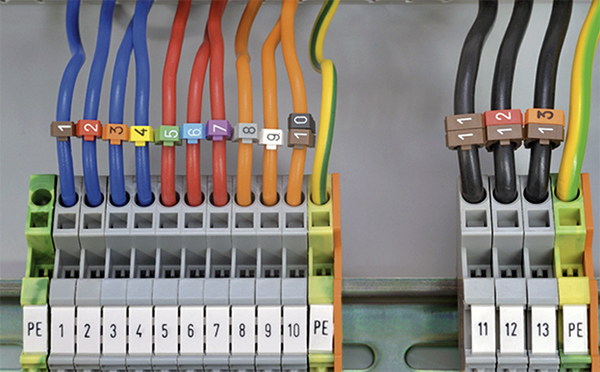
Panel labels
For every electrical breaker, there must be a record of which module(s) (modules are actuators and actuators are modules) it supplies power to. In turn, the module will supply several lighting circuits, heating, or other devices. These must be noted against the electrical breaker. If, for example, an electrician attends site to change a lighting driver, they should be able to work out easily which of the breakers should be turned off to make the circuit safe to work on.
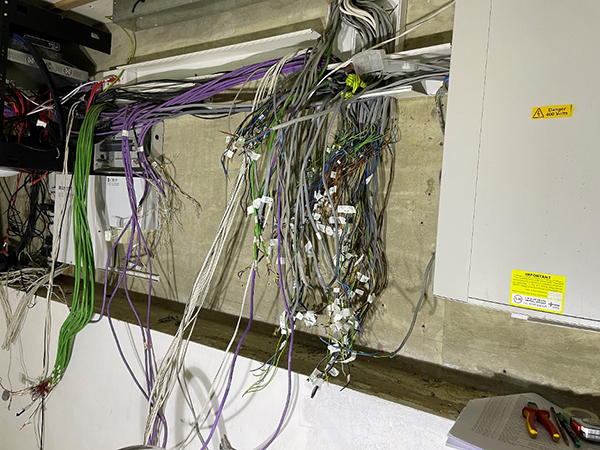
The second part of this puzzle is to provide information about where on a particular module the circuit is connected. Can the electrician or homeowner manually turn on or test the circuit? In providing this information, you eliminate the need for control via a wall switch or any form of programming, therefore providing the means by which the electrician can prove that they have successfully rectified the problem. Without this, people are simply guessing and may inadvertently turn on something that is part of a sequence of devices, for example, the manifold pump gets turned on but not the manifold valve, causing the pump to be under stress pumping against a closed valve until the next time the program triggers those devices on or off.
There is a notable example of panel labelling in a recent KNXtoday article. I’m sure everyone would agree that they’d prefer not to have other trades poking about in our panels, but equally, we don’t want to be called out every time a lighting driver has to be changed or a fused spur blows its fuse. Unless, of course, you have an electrical arm to your business, in which case you absolutely do.
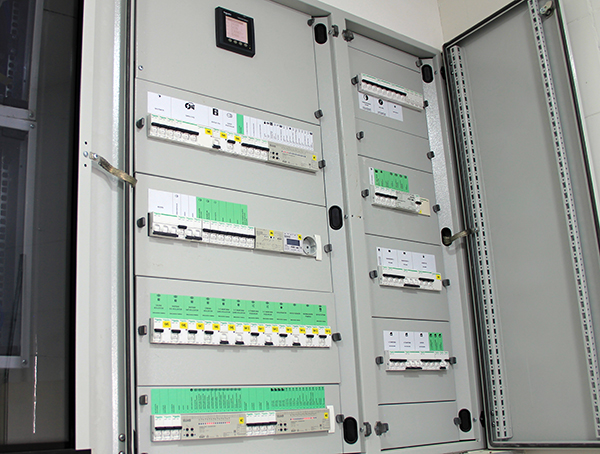
Electrical safe isolation and multiple points of isolation
Any competent electrician will be familiar with the practice of safe isolation. Here are the rules.
THE RULES OF SAFE ISOLATION
• Obtain permission to start work (a permit may be required in some situations).
• Identify the source(s) of supply using an approved voltage indicator or test lamp.
• Prove that the approved voltage indicator or test lamp is functioning correctly.
• Isolate the supply(s).
• Secure the isolation.
There are times when modules may be fed by more than one breaker due to current limitations or practical design considerations, such as a half of a module feeding downstairs and the other upstairs. If our panel, a module, or indeed a device is being fed from more than one supply, then we must warn people with a ‘More than one point of isolation’ sticker. It is not uncommon in a plantroom to have the permanent supply to a device, such as a pump, to be fed via a fused spur but the switched live to come from the KNX panel. I would argue that the fused spur should also be fed from the KNX control panel, but this is not always possible.
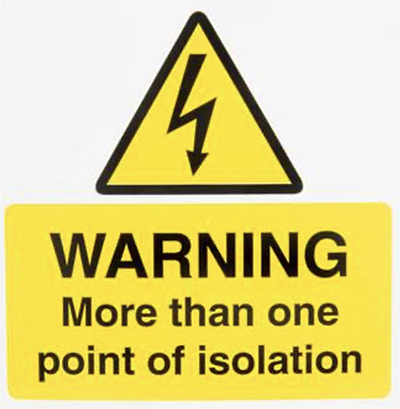
Conclusion
On the very last day/visit to a job, can we look around at the information we’ve provided and be satisfied that any competent person who came to work at the property would be able to carry out their job safely and concisely? If they have to spend an hour on the phone to us just to change a light fitting, we probably haven’t given them enough information. As I’ve said before, KNX is the engineering Lego that makes almost anything possible within the home, but what each module does can vary from installation to installation. As a result, it is incumbent upon us to ensure we have documented and labelled our work accurately so that others can work safely.
Simon Buddle CEng MIET, is a consultant for Future Ready Homes, a specialist in BMS and ELV services system design.